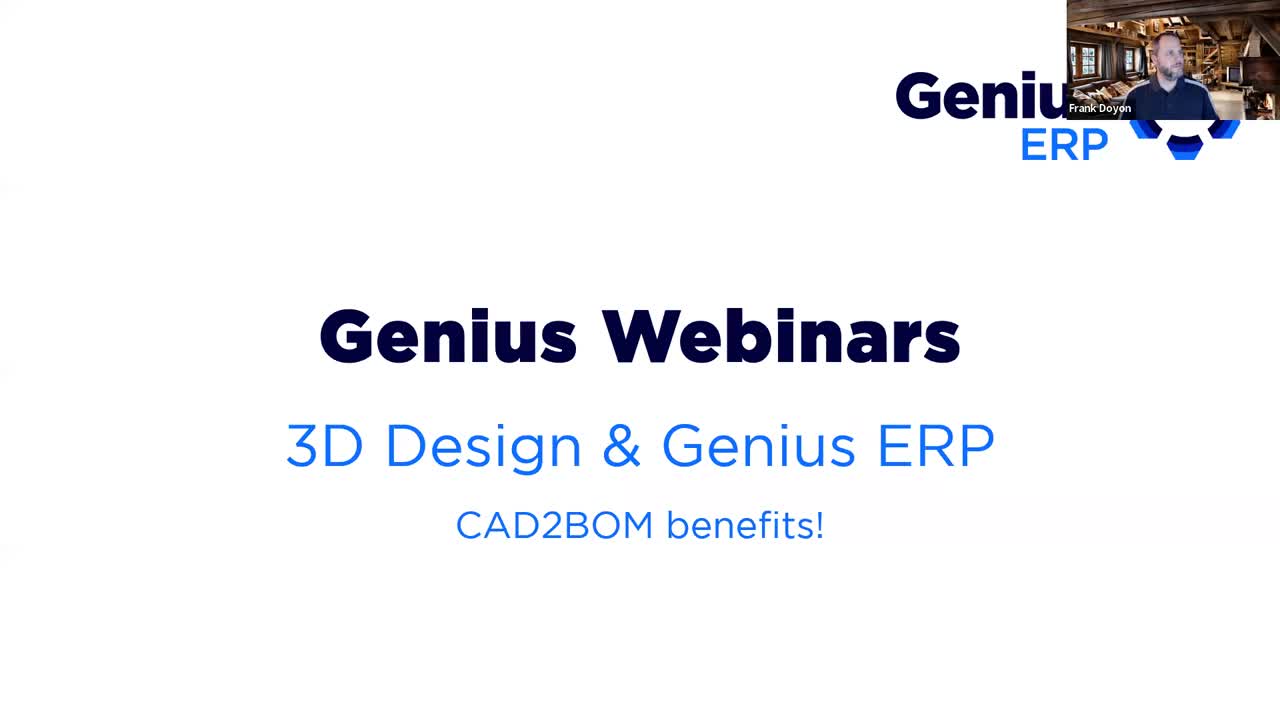
If your CAD system is not fully integrated with your ERP system, it’s not only frustrating, but it costs you time and MONEY. Watch our free webinar to learn how Genius ERP’s CAD2BOM connects your CAD system with Genius, improving engineering efficiency (and stopping your headaches).
See how Genius ERP’s CAD2BOM allows you to link to SolidWorks and Inventor applications to automate the creation of BOMs, items, and routings from a CAD model. CAD2BOM helps custom manufacturers save on engineering time and improve communication between departments.
Read the transcription
Welcome to another Genius webinar. We’ve been in a habit of trying to doing one per month, always about mid-month in the afternoon of Wednesday. That’s our classic. So thank you if you’re joining for the first time. Thank you if you are a returning attendant. So we’re definitely glad to see you coming and joining these sessions. So today, the topic is going to about how do we take design and 3D design tools to the ERP. And for sure, we’re a genius ERP here, so we’re going to be talking about the tool, the CAD to BOM tool that we leverage to have a synchronization between CAD and ERP. For sure, we’re going to talk about some of the benefit, but I’m going to start by, and let’s look at the agenda first. My name is François, but you can call me Frank. I’m going to start with a small introduction on who is genius. It should take about four minutes. If you’re listening this post-recording, you can skip through, perhaps, if you don’t want to learn about genius.
Then we’re going to hit, what is the tool, CAD to at Genes. Is it really for you? Why would you use it? Then we go into a small demo of how it works. Then we’re going to be talking also about how it could come in and solve a whole lot of headache in the engineering to order world. Whoever is conceiving or designing as production needs to start, we’ll be discussing that portion for sure before the end of the session. That’s a really great topic here at Genius. Welcome, everybody, again, and let’s hit this This is our first webinar. All right, first of all, who’s Genius? Well, Genius is an ERP for manufacturers. We’ve been serving manufacturers for more than 30 years. We have more than 100 employees at Genes for more than two or three years now going. I’m proud of it. We’ve been serving all North America. That’s really our market so far. We have 10,000s of user using the software, and this is the heart symbol, but really it is, I think, one of the biggest highlights in this page is we do have a 96% retention. What does that mean? Well, customer that comes to us, they stick.
They like us. We really give a journey to our customer when they join us. We are there to assist. We really want to have our product focus to the needs of our customers. So we pride ourselves in getting a good fit with our customers. 25 % compounded growth. Now, this has perhaps been shifting between 23, 24, and 25. We didn’t have a three last years. But even with COVID, we continued growing. All right, I’m going to brag a little bit for sure. We’re pretty proud of what we’ve been getting as results here. These are different websites that helps people select collecting ERPs for their market, for the business. We’ve been pretty well ranked in pretty much all of them. You can see even the Gartner chart here that is pretty popular tells you that we sit pretty well compared to competitors as far as customer satisfaction and usability of the software. What makes genius ERP unique compared to other ERPs in the market? Well, first of all, I said it, we’re built from manufacturers. This is our niche If you’re doing a whole lot of sell, of distribution, we might not be the good solution for you, but if you’re building, fabricating, this is definitely the good place to be sitting at.
We have a complete quote to cash offering, meaning that we cover all sorts of things, all sorts of need. But again, really focus on these specialty builds, so a lot of engineering tools such as the cat to bomb integration. We have also a leading edge in scheduling. It’s been around for three, four years now where we have the entire… Like, constraint DBR concept within our scheduling to help really line up orders, prioritize them, reschedule globally your shops. There’s quite a few tools we’ve brought on board to our ERP. Business intelligence, for sure, dashboarding. We actually had a really nice addition to our tool set recently where we have actually dashboards online where you can go and share with your colleagues, create your own straight into our tools. That’s actually so you can now be remote and looking at all these KPIs. A little something about our coverage. So again, I mean, quickly, quote to cash with things like cat to bomb, and all this is really part of our core offering at genius. There is a few things we’ve added along the way recently, and we say latest release, but this is perhaps a year old, this slide.
We have a Field Service Edition, tools for people on the go, dealer portal for customers to log in actually enter their own request and track their own orders, warranty management, so post-sales services, for example, and knowledge based on equipment and on fleet of equipment or items that your customers want to track, quality control, and all sorts of other offering. We can get into these if you have more questions. How can you get to use? If you are interested in getting the software, how is it deployed? How is it installed? Basically, we We have two offerings, but different means here. You can buy it or you can rent it. So whichever way, we will install it on your servers, if it’s on premise, on your side, or if you’re having a hosting on the web, that can also be done. But we also offer our cloud solution, meaning we manage your hosting and it’s a rented means of renting and accessing out. Super important here to say how the onboarding works. We do have implementers, consultants, all that. But I’m thinking of existing customers. I’m trying to see through the list here. I think there is at least one or two people that I know of that is our existing customer of ours.
So hey, hello. I think John is one of them Craig, perhaps. I’m not sure if it’s that, Craig, but anyway. So I know some of you are existing customers of ours, so welcome back. And there is a platform today that’s called genius Academy. It’s been around since just prior to COVID. No, we didn’t know about it in advance, but it seems we were well-prepared. So this is an e-learning platform. You can go online, register to your courses, find courses that interest you, and learn at your own pace. The advantage of this is really where you might have turnaround, you might have new people joining. You might want to try to see or foresee if you could use the software in any other way. So digging into some of these bite-size video or some of the document materials we have on there could really help figuring out how to use or how to best use the software. On top of that, on that same platform, we do offer what we call Canteen, Ask the Expert Session. This is a nice example where you see Sylvain, what am I calling, giving the Wednesday Canteen, who’s logged in and there’s four different customers that have joined with their questions.
Sometimes they share screens, sometimes they answer each other’s question. It makes for a nice discussion with perhaps similar customers that come and join these canteens and ask their question, How do I do this? Is there a better way to do this in genius? And so on and so forth. And these are free access to our consultant three times a week where we have that platform, and people can join. And that’s part of the academy offering. All right, let’s get back to topic here. Now, I’m hopping right into this. What does cat to bomb means? It says it in the word cat to bomb. So it’s a transfer of information between the cat drawing. And in this In this case, we’re really talking about 3D drawings, mechanical in solid works or inventor. This is where the cat to bomb tool sits, exists. It allows you to push information to bomb, and In this case, BOM, I’m going to say bill of manufacturing. I’m really taking pause on the word manufacturing, not bill of material, because it does include material, but it also includes routing steps. Operations that will take place in the shop, sequence of event that needs to happen or that I need to track.
There will be also more stuff such as raw material or third-party services, expenses I need to also plan at. Now, needless to say, this tool is not only one direction. The name says cat to mom, but it’s from and to. That means I can actually bring back information also from the ERP back to the cat drawing. We’ll discuss that further in a moment. But just so you know and you are aware, it’s not just This is a one-direction tool, it is bi-directional. Again, so far, we have this tool in Solidworks and Inventor 3D. All right. Now, for those of you who are wondering, am I sitting in the right place? Is this for me? We’re going to go through the reason why people are mostly coming to us and in need for this tool. We said it, we want to bring that in the ERP. The first and low-hanging fruit is probably, I don’t retype all my materials. I don’t want to output them, import them or whatever. I want to hit a button, see a screen. What’s new? Do I want to push it? Yes or no? Hit Save. Done. Yes, that’s what the tool does.
So first low hanging fruit, there you go. If you’re in that type of condition that this tool is for you. Second of all, well, there’s also other little fruits around I’m going to pick on duplication. It is a synchronization tool. You’ve done an update, a change, you want to push something in, oh, this already This is a new component. Wait, I already have this component. The system gives you warning and tells you color codes and stuff like that. Thumbnails that will tell you you’re adding, you’re updating, changing. You will be aware of that. Paper piles. Now, a lot of our customers will do this today. They don’t have a system or they might not have any ERP prior to being our customers, I should say. They were printing out drawings and packets of paper, then would assign that to somebody in charge of operation. That would file it or pile it against work orders or travelers to issue to the shop. So a lot of paper shuffling, a lot of piles, a lot of paper. So for sure today, with the tool, you will be able to, when you do your push, keep a link between the drawing and what you’re issuing to production.
So that means on the shop floor, also with our tools for shop floor, live people could say, I’m working on this task. Can I see the drawing? You can click and view the drawing. So we keep links between drawings pushed in the system and what exists in the system. So yes, it allows to go paperless if you want to. I love this picture. Yes, I do have young kids at home. I love the comparison here. Have you ever gotten in the situation where you find two travelers the same thing, but they don’t look alike? Which is the latest version? What have changed between both? Or you’re managing engineering versions, and we’ve done a revision, which one is issued here? Is it A or B? Really, we can help out with that. Again, it is a synchronization tool. When you’re about to look at what a drawing is, what is currently in genius, what would change if I synchronize both? What would I update? And yes, I can also keep revision numbering alive or version numbers also alive through this. Now I’m leaving you with another topic that will be my last topic before we end this presentation today.
But perhaps you’re also in one of these worlds where I’m going to take a typical example here. We have gotten an order from a customer. We’ve given out 10 weeks to make it. But basically, what really happens in our factory is engineering takes eight weeks to get drawing approved and done, and then we are chasing our tail for producing in just two weeks. Does that sound familiar? I don’t know if there’s no mic, but I’m thinking it might be familiar to some of you guys where sometimes we’re engineering, or design carries out too long of a lifetime or lifespan. And now we’re trying to start production before we even have our full drawing approved. So this is probably 90% of our customers that are into design to order. We do have means of facilitating that in genius where you can have simultaneous design and production happening. I’m not saying we’re producing what you’re still designing, but we can It definitely facilitate a portion of your design that is a bit repeat from one to another. The frame is always the same, but the entire machine, conveyor size or whatever it could be, is different every time.
So issue what’s known to the shop, start working on that design, and later on, you’re going to be pushing out the approved section, either by work break down or until you get whatever is specialty design done, the production can at least start on everything else. So compared to other ERPs, this is a differentiator for us, so we’ll touch base on that later on. Now, about the fact that this genius CAB to BOM tool is bi-directional. For sure, we’re going to be able to catch back information from the ERP going to the CAD. Now, I should say something before we go there. I mean, nowadays, a lot of things happen when production We’re changing some stuff, but it doesn’t necessarily change the, what’s it called, the form-fit function of the design. We don’t necessarily need to change the drawing, but because often we see this all the time, like I said earlier, people are using drawings as their master design to push information to shop floor. Well, every little change that happens about a spec, about a raw material, piggybacks to the drawing, we need to edit, change the drawing, revise it just because we’re changing a few specs.
Often, we wouldn’t need to go into that extent of doing revision and all that. Again, things can be changing on the shop floor, and it would be easy through our tool to just synchronize that information back. First thing I would see is as easy as I’m issuing a request for quote, and then maybe going out in the world, we figure out that there are some specs that are off when we created for the first time these items. It’s a way for us to leverage the power very early on in the process. I’m still in design, I’m wondering how this is going to cost. I can push only some components to genius, leverage the estimating tool, the request for quote tools, and piggyback the information to my drawing to finish my design. That could be one of the reasons why you would use information back and forth. Second of all, I love this one. I’m an engineer myself, so I allow me to play that joke as an engineer, but we often are in our own little island of terminology when we speak engineering. So yes, Yes, with this tool, you’re able to create new components, new part numbers, and stuff like that.
Often what happens is engineering pushed their design in, and then the buyer turns around, tries to get a quote or tries to get these new components out from the market, and the entire industry speaks another language, and we get lost in translation. What type of motor? A flange of something? You’re able to change description, change specs, adapt things in the ERP, and synchronize this back to your drawing. So please, for sake, if we reuse this drawing in the future or if you do the future update, we don’t keep pushing that same lost in translation text in next design, but we keep it up to date with the industry verbiage. So that’s one of the reasons we’ve done this in the past. Oh, and for sure. We said that there’s so many things that could affect the specs, the properties that we put in our drawings, but not necessarily affect it form functions. So that’s going to be another great opportunity that any change as an assistant can piggyback to the drawing. So that next revision or next time we do a similar design that we piggyback on that drawing, we have up to date information in our drawing.
In a nutshell, it’s pretty much why or where we’ve seen people come to us to use genius cat to bomb. So, yeah, it’s time for a demo. I’m going to hop into the system and show you a little bit how genius cat to bum works. We’re going to hop into solid works, and then we are going to hit… Give me a second. I think there is questions. No, it was a previous question. Perfect. So again, I think at least one person have joined since my intro started. Please use the Q&A section if I don’t have time to answer, we will piggyback afterwards and look at the files and all the questions to answer. I’m going to go, not in genius, but in solid work, straight in there. Here’s a little drawing we have in solid works. First thing is, yes, it applies to 3D design in solid works and Inventor. I chose solid works today, but yes, it does apply. It is very similar in the way it works in Inventor. It adds a new tab that’s called geniusETM. That’s our catabung tool with some of the buttons in there. This is where it lives.
Same thing for Inventor. If I forget to talk about it, I think in Inventor, it actually leverages the IA properties instead of the custom properties of solidworks. It’s an add-in. Then the other thing I should be saying here is it will help us synchronize thing between what exists in the cat and what exists in genius. Let’s do that. I’m going to actually hit the corner button here to start the genius CAB to BOM tool. It’s right now looking at… Oh, let me do something. This is still French. I did a French demo this morning, so I’m going to cancel this out and log under English user, so we don’t have these French windows coming up. All right. I’m going to log under my English user. Let’s do this again. Launching tree. What it’s doing right now, it’s figuring out what you have in your CAD drawing and doing a tree view representation of the bill of material. That’s what’s going to come up on screen. It’s I’m also looking at data in genius to be able to sync in a moment. Let me put this full screen. Again, this is a window that lives in the plugin in solid worse or inventor.
It’s not part of the genius ERP. It is really that entity itself that’s in the plugin. Now, when I have this, this is the entire content of my design. I could be pushing only one component. Maybe this is the only thing I’ve designed so far. Maybe I need, like I said before, a request for quote. I want to sync that in the system, leverage the info to do a request, and bring the information back. Now, I could decide to push a complete subassembly that would make sense. For example, if you’re in design, everything else already existed, then you came into your drawing and did a special version of that subassembly, you might only want to push a portion of your drawing. Let’s sync everything for my example today. First, I’m going to go into Billing Material section. We’re going to go to Routing in the second portion of my demo here. All right, now we have some indicators. See here, there’s a little arrow that’s saying this is going to be refreshed, so that means it already exists. Let me show you this. We have a visibility into what’s in the CAD drawing and another visual here to what is in genius.
As you can see, the parent component already exists in Genius. Remember, Genius is able to create new item numbers in the ERP. The counter bomb is able to create new items in the ERP, and it’s also able to push your bill of material in routing. In the ERP. Right now this item already exists. It might be updated here, and now we can see the little plus sign. All of these components are going to be added to the construct of the bill of material. See, some of these subassemblies already exist, so they will not be created right now. If I expand one of these sections, we can see what the master files look like. In this case, I can see that this item already exists. What Kutma has to tell me this is, well, first the color code here is gray. We do have a color code that tells you if it’s going to be added not. But you can see here, I actually have 12 on the handle right now in my inventory. I’m able to see that information straight from that synchronization window. Now, in addition to that, I just said create items, create build materials, create routings, but it also allows you to piggyback on your properties and leverage that to create raw material structure.
I’m able to say that to do this component, I’m going to require a certain surface of plate, a certain linear foot of a flange or tube, so we can actually specify raw material right in there as well. All right. What happens if I do Edit and Save? It is going to push the information. See, it’s rendering the raw material as components, putting them under the proper parent and pushing all the information into the ERP. Now we’ve pushed this into our BOM library. What is a BOM library in genius? It is basically a repository repository that says when I want to do a Pallet card of this number, I have this nomenclature. If I do a parallel here, and I actually left everything in French open, so let me close this off. Really sorry for everybody attending right now for that. Just going to log in to genius in my English user. What we’re going to do, I’m going to go straight into my BOM library and look at the the Palette Card component that we were just looking at. 0934 something, and it’s the Palette Card here. We can see that after doing the push, I now have the entire structure right there in genius at my fingertips, so I can leverage it to push production, use to do estimating, request for quotes, and all that.
The next step I wanted to show you is where does the information reside? Let’s a little bit more detail into the CAD, how this is structured. If I close this back up and go back to my drawing, let’s go to a specific component. Let’s say I want to use one of these little rollers. Here it is. Let me open up this roller here. Here we go. On one of these components here that I have to build, if we look at the property from that specific drawing, you can see I have a family of product, I have a part number, a description. These are all properties that we’ve added or maybe you’ve had before that we’ve mapped out to sync to genius. You can create your own, we can leverage the one you already have if you want. There is a mapping tool, and this is something we would go through in your original implementation of this tool. Normally, we don’t really change it afterwards. That mapping is done once and then you keep on using it. If I click on the mapping here, you’re going to see we can leverage some of these property names for different fields that are existing in inGenius.
The minimum requirement here is pretty low. If you’re worried about onboarding with this tool, it is pretty low maintenance, meaning that when in inGenius, you are creating a part number, for example, you can only specify the product family and the part number, and you can be good to go. The family itself entails how it will behave in genius. This is a purchase component. Is it tracked by square foot? Do we track serial numbers on this? Now, all sorts of be it can be inherited just by choosing the family. Don’t worry, you can also sync a whole lot of other information, thickness, material type. There is a lot of other fields in there that you can leverage as well. This is how we do the mapping here. On top of that, we were going to talk about routing. Let’s take this component as the example for my routing. I’m able in genius to define templates of steps that could be happening in the shop. Then I can flag them into one of these properties so that a CAD to BOM can push the proper routing steps to my bill of manufacturing. Let me show you what I mean.
If I go into my library in genius, we’re going to look into Cut and CNC That’s one of my template. You can see here, cutting CNC. If I go in grid mode here on the routing steps, you can see that there’s half an hour of cutting and two hours of machining here. These are my two steps that we have planned to stand out in this template. It could be many more. Again, some people use this with very precise time because it’s really recurring from one time to another. Some of our customers were just putting the proper sequence of events so at least they can track the proper sequence to the shop and track which one is done or not. Then we can tweak out the times. We don’t need to have them set properly in the template itself. Let me show you what I mean. I go back to Solvay. This property is tagged to that same template. Let’s go look at it. My property scheme, this is routing template, short name for it, and here it is, CNC or cut CNC. If I hop back into synchronization with genius, only going to take this small component for now for the sake of the example.
All right, so now we can see this component that I want to sync in, and let’s go into routing. Now, let’s put this full screen. You can see that because I have identified my template, it suggested me, I’ll go Edit here, to push in cutting and manufacturing, half hour, two hours. But I could override this. If I want to, I could put this an hour if I want, and that would push that hour in to our bill of material. Now, when I save this, again, let’s show genius. Right now, because we did the push and that was one of the component in there, it already has that submaterial the raw material on it. But if I hit save, now it’s going to add the two operations, the two route steps. You can imagine for an entire construct here, tag some of these templates all over the place. When you do your push, material, routers, everything goes into place. What am I missing here? The other thing that happens as well, since I’m in here, in genius, if I look at the result for this, this is Let’s go 0934, and it’s component 201106. Let’s see, this is the end result in genius in my BOM library, and I’m able to see on the item itself, when I did my push, I did put a setting that automatically sinks in also a link to the CAD drawing.
That means if I get to Printing Travelers, I’ll have the option to print document as well attached, Or probably the best outcome here is with genius, we have a nice web interface for people in the shop floor to clock time, consume materials, view attachments. If you do have a eDrawing or one of these free 3D viewers, you could click on this, view the document without having the need for a big packet of paper on the shop floor. Just a few options that we put to the table at the same time. Sorry, I should have muted that. All right. If we go back at this point to our presentation, I’m just trying to piggyback to my PowerPoint here. We were at the next slide here. We were doing the demo. At this point, I want to piggyback on why we would use the tool, but I’m not done. I’m going to go back to another portion of the demo in a moment to talk about this simultaneous design and production happening and how we can sequence them to be concurrent a little bit between engineering and production. For sure, that’s going to be my next topic.
But again, to remind you why people are using CAD to BOM, we need to push information without having to retype anything into the ERP. Now we have extendable information, Intel, that we can just click a button, throw into production, throw into scheduling, have MRP giving us right away the dates and everything we need for procurement to align with production to happen in a nice flow. We have documents already linked, so we can almost go paperless if we want to in some cases. We’ll prevent a lot of the duplication issue. Again, it will help us to do our control version, and we’re about to do revision or changes. It will also help us because we can hit back a drawing, see what’s currently in genius, what we’re changing, what are we actually pushing in as revision version? We’ll talk about this in a moment. For sure, coming back to genius, I mean, outcomes, again, since I can push and bring back, I can use this to create new components, validate information, request for quote, bring back the information, do adjustment to terminology sometime, and also helps to, I’m going to say, consolidate or bring back information on smaller changes that might not fit form function of your drawings.
All right. No questions so far. Again, don’t hesitate, please. Write in your question if you have any. I’m going to be very happy to turn around and give you a bit of my time to answer your question thoroughly. It’s a complex ETO project. What I mean here is my next topic is really concerning people that hit design for a certain time, and that will need production to start before the full design is completed, or will need to go and revision after production has started. That could also be a case. Before I go into my demo, I wanted to take a moment to explain Genius ERP structure that might not be similar to what you’re doing today. Because of the terminology I’m going to use, I wanted to put something on screen. Let’s talk about what we’ve seen so far. I was leveraging the BOM library where we were pushing information from CAD to BOM from our design. In Genius, what is a BOM library? You saw it, I was looking up a part number and I had one matching bill of material. I could have been revision A, later on maybe revision B, but I’m always having a live version that is active at one moment.
That’s our BOM library. What happens when you start working on the quote? Well, typically, if you’re into design to order, there’s something that’s going to be different from your library, from your original template that’s going to change. When we start doing a quote in genius, we don’t actually change the BOM library. We’re going to pull information from the BOM library to create what we call an engineering life cycle, a version control dedicated to our quote or order moving forward. We’re going to start working on that, probably to estimate first, so we can throw in some rough values in there or just to estimate. And later on, we’re going to start working on design. So probably we’ll be having already version from the sales cycle. And then at some point, we’re going to start working on our engineering or release that’s going to hit production. When we’re ready, we can actually push a sales order out from that version, that engineering version, to a job order. And that’s what we leverage great job, work orders in the shop, engineers. That’s our structure. So that bill of material structure becomes that’s workable, that cost center, that tracking of material and all that.
All right. So I’m telling you this because at some point in genius, there’s options for you, meaning that as soon as we have a PO from the customer, what I would suggest is create a job order right from the start. It could be empty at first. No requirement, no nothing. Well, this is where in the kickoff, you might argue with your engineers, with your project manager and say, You know what? I know we’re going to need this motor. We don’t have it in stock. It takes month to get it. We can have a preliminary list of components that we will need to supply upfront. Yes, that information can be pushed from solidworks, but at some point, we will issue a list of long lead preliminary listing for purchasing to take action, and we can give an estimate date on that as well. There’s more things in genius project management milestone that can help even do a high-level schedule day one without having a build material. Now, most commonly with our customer, there is a portion of the build that is reusable that we could start working on. Might it be the base of the machine, the frame of it, or a certain conveyor structure, there’s usually a certain portion that we can start working on pretty early.
Normally, this is what we see. We see an early release that would have empty breakdowns at some places. We have also some preliminary listing of things that will be part of a later release, but we know we need to purchase early. This is what can happen in in genius. Then we start having approval with customers and we are pushing the drawings into a new version because now we can keep all iteration of changes in genius as these different engineering versions. We can compare any one to another at any point in time. When I’m ready, when I have that release that is really we’re saying there’s this new design, the motors in there, I want to push it to production, then I can sync with whatever is already in the job. This is a pretty big differentiator for us. The fact that we have versions that are dedicated to an order or quote of engineering, and the fact that we can actually synchronize or push new stuff into an ongoing job. In other ERPs that I’ve seen, personally, as soon as you would clock time or start registering material to whip, it would freeze the job structure.
You could not be doing any changes to it. You’d almost have to cancel it out and doing you on if there were any change. In genius, we are capable of tracking these, I should modifying a job after it’s been released. All right. That being said here, the point is there’s something that’s alive and genius to help you guide you through these changes, these new push. In the CAD to BOM world, that’s the topic today, that means that I can use CAD to BOM to update my BOM library, update my templates, but I can also do revision tracking if you do more of an R&D drawing. If you are really using it for design to order, you can push into any one of these special builds with a unique build every time without impacting your BOM library for next order. Sorry. All right. Now, that being said, let me show you a little bit how that works. Now, what I’m going to do next is I’m going to show you an existing order in genius. Probably some of you have never seen this, so it might look a bit complex. I’ll explain the structure for a second.
Then we will hop back into and let me show this again. I’ll hop back from the job order. I will open the BOM or engineering lifecycle. We’ll create a new version and push stuff from cat to BOM that we will then synchronize with ongoing production. It’s a couple of steps here, but follow me along. I think you’ll get the big picture of how we use cat to BOM, how we can manage different versions in genius. All right, so let me go into what we call the work order management. That’s really the heart of genius. This is where we manage our job orders. This is where a lot of the magic is happening. If I go on this job here, now I’m making this full screen. Let me explain on the left side here what we’re seeing. This is the environment, again, where we create our job, our work orders, and this is what you’re seeing. I’m seeing right now. I’m fabricating a capping machine. This is job 10311. I have a work order that says I’m fabricating this specific equipment. Below that, you can see there are activities, assembly, testing, shipping. So the little man or persona that you’re seeing in thumbnails, they represent routing task, operation with time behind it that will help for scheduling.
And now I’m going to need to do a sub-assembly here for a frame, another assembly here for bearing tube, for example, another one here. So every time you see these little barcode, it means it’s a work order or subproduction that’s happening. So playing around here a little bit with the view, but you We understand that these are subproduction that are required to be done prior going to next step. Yes, there is a logical order of things happening in genius as far as sequencing work orders, task, and all that. All right, that being said, what are we seeing here on screen? We are seeing something that was created out of one of our engineering document. Let’s hop back into the engineering document to see the structure. I’m going into that document, 81, and you can see there’s one I have this version listed. If I increase this a little bit, there’s version 103 that we’re working on right now. I can take this version and say, Now it’s time to make something new. I’m going to be pushing another component into my machine frame so that we can release it to production. There’s something we forgot to put in there that we need to fabricate special for this time.
I’m going to copy this version. I’m going to say that I’m keeping the build material, keeping routing, budget objectives, and all that. You can always cover that on further question for another session, but when we copy a bill of material, we have options of what we’re keeping around or not. This is a great example where maybe you’re starting from a sales bill material that could be a bit of gibberish just to get to a pricing to when you start your engineering structure So you can empty it out just by unchecking the bomb and routings and you start fresh vanilla. Now, in this case, this is going to be my future version that I’m going to sync with production. I’m going to be flagging this as my official engineering version from now I can see now I have the original version and the new version. And if I put this a bit larger, you’re going to notice that I have final sales version that was ticked on 103, and final engineering version is going to be this one. I probably just need to refresh your Final engineering version is this one here. All right. As I said, we’re going to go back to solid words, work on our drawing, and synchronize that to this frame section, so I’ll be able to synchronize that with production.
Let’s go back to genius ETM. Remember, I was already into this little roller. I’m going to just piggyback on that same drawing and use that same information. Let’s start with a build material. But this time, instead of pushing into the BOM library, I’m going to configure this to push to my injuring document. I remember the number was 113. Here we go. Now, if I don’t say anything, it could override the entire structure, In this case, I want to push under one of the assemblies that’s in there. I’m going to push under that frame assembly. It’s just going to add to the existing structure. Here it is because I chose the proper document number. It’s showing to me on the left what it is, and we’re now going to be syncing under that 101. I’m going to push this with its raw material. Let’s just edit Save. Now, before it refresh, it usually ask me if I’m still synchronizing. Yeah, I’m still synchronizing with this version. See on the left-hand side, our little roller appeared with the raw material of the rod. Now, I’m just going to push it a step forward. Let’s do the same thing for routing.
You remember we were leveraging our cut to CNC task, so I’m able to do the same thing here on router, and I’m going to be able to edit, save, and push this in. And save. Now we’re going to see the two routing steps appear also here on the left. There we go. If I go back to Genius, because this is the view from the engineering screen within the CAB to BOM in the SolidWorks plugin. If I go back to the engineering screen in the Genius application, let me just refresh, and you should see appearing here that subsection for the roller that we’ve added. Now I had an original version that doesn’t have it. If I go back to 103, it does not have it. Then if we hit 113 again, it has it. All right. Since 113 is the current version that I’m supposed to use to synchronize with ongoing production, when we’re ready, we can go into this job order and ask the system to suggest to me what we should be synchronizing between the engineering section of genius and the production section. Now, also, genius is telling me, Oh, but wait, are you where?
We’ve changed a version since you did the last sync. Do you want to continue? Yes, your advice. Engineering has created a new version, and now you’re pulling from a new version. Here’s the novelty here. With these color code, the system is telling you this is what I’m seeing new in the engineering structure that I could be pushing for you in production. Now, there’s a big confirm and change, or you can go and manually pick the one you want to do. I’m going to hop into some of the features here. I’ll hop, skip some of the features just to show you that I’m able to just push this into production. There are some other things that we could have discussed here. The fact that are we creating a PO? Are we just picking from stocks? Should we be creating more of a replenish management order, or there’s a lot of questions here that we could always argue on a sidebar, on a side discussion, if you’re interested to know more about how genius decides if we are to create a work order or not. The point here is we leverage genius to create and manage We’re able to push from our CAD drawing into any of the version or in the BOM library.
Then I’m able to sync from whichever of the version I have to ongoing production to keep the flow going to the shop at my own pace. All right. I thought it was another section. Questions. I guess I’m going to flip this. I’ve seen Even in other webinars, when I hit the question mark, people are leaving. So just a second. Just want to give you a little insight. Next month, again, mid of the month, we’re going to have another webinar on smart scheduling. These are two webinars that I redo almost yearly because it’s a big differentiator of ours. I try to pimp it up, change it a little bit every time, so there’s a bit of new things to tell you about. But the next one is going to be on October 12th. If you’d like to join us, I’d really appreciate it. If you are interested in knowing more on any of the topics you’ve today or about genius, if you are already in contact with someone from our company, please piggyback to them. I am known the company, they can reach out to me if I’m needed. Yeah, there’s a question here. Larry, you’re asking if we will We have a recording out there.
It’s not going to be by email, but it will be available on our website, and that’s a great question. Let me show you where it’s found. So in the Genius ERP website, so it is geniuserpcom, you’re going to find resources that we have our webinars. So every previous webinar recorded is on here. So you’re going to find different topics. If you’re looking for last year’s webinar, it will probably be on there. I think we removed it in the interest that people would come and listen today, but we’re going to add them back, the one from this year and the one from last year for Kata and will be appearing in next week or so, or if it’s not date on our website. My pleasure, Larry. Again, any other question you can think of, I’ll leave the chat open at least for two minutes. You have time to write your question. I will get file with all the questions that were not answered, so I will be able to answer you back if there’s anything that left standing. If you don’t have time, you can reach out to sayhello@geniuserp. Com, or this is my personal contact here, fdoyon@geniuserp.com. Thank you very much for joining.
Get your eBook Scared to implement a new ERP?
"*" indicates required fields