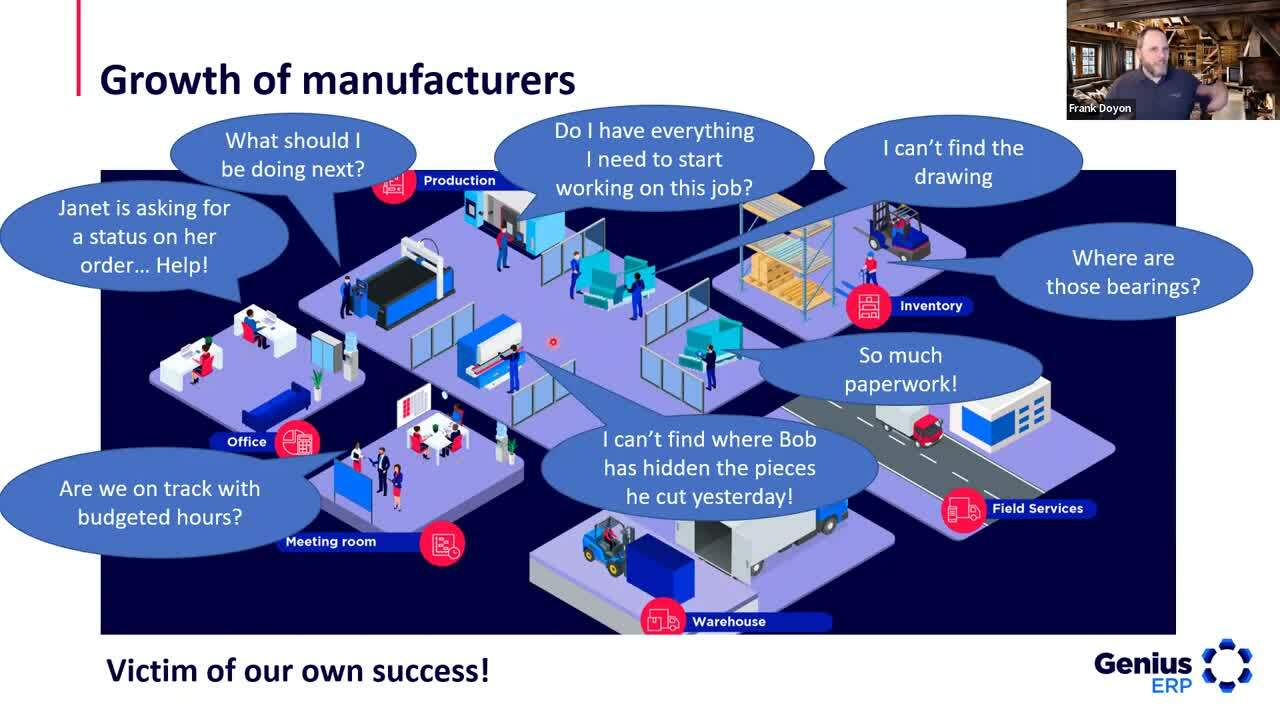
Learn about the benefits of software integrations with Genius ERP, and you have probably heard buzz words like Manifacturing 4.0, Artificial intelligence, Industrial Internet of Things, etc. These are words that make every entrepreneur dream of having seemless integration between across their ecosystem to streamline the manufacturing process.
But how do I get there? Well the first step is to get rid of paper. In this webinar, we show you how Genius ERP enables a full Paperless environment by providing significant shop floor tool for every role in your organization. From time clocking to material picking to WIP tracking, we have it all!ow they can enhance your business processes. Discover the real-world advantages of integration through a case study presentation of nesting software Sigmanest and Genius ERP.
Read the transcript
Thank you for joining. My name is Frank. I’ll be your host today for another Genius ERP webinar. And I guess maybe some about me first is I’ve been with Genius more than seven years now, going on eight. I’ve been implementing the software. I’ve been training people to use it, showing it off for cells, really any way I can try and help our users to feel more comfortable with a tool. I love playing guitar. I got two young boys, but the topic is not me today. Maybe we can feel more at home now that you know me a little bit better. But the topic today is really how to connect Shopfloor with Genius ERP.
It’s a narrow statement, I think. What really we’re going to discuss here is how to get everybody connected and working off of one system and not having, well, exactly what it’s saying here is an office crew and a shop crew or one company we want to work together. So that’s the point where we want to get at with today’s presentation. And behind the scene, there’s a topic that is omnipresent here. It’s the 4. 0. We are in a new era of technology, and there is a lot of information going back and forth, and a lot of things are beginning to be smarter and smarter. When I say things, I really mean physical or computer computers. We’re starting to see intelligence come in here and things or people taking more advised decision with a flow of information. Really, this is the entire topic for today. What I’m going to do is try to move to my next slide. My little persona here, robot. All right, so the topic, again, connect your shop floor to your ERP. How are we going to cover this today? Well, let me go through some of the objectives. As I discussed, the Industry 4.
0 or Manufacturing 4. 0 is right into the topic that is to the core of our discussion today. What is it? I mean, you See the little graph here. It talks about connecting everything. You probably heard some buzzword like manufacturing 4. 0, artificial intelligence, industrial internet of things, IoT. There’s a lot of little terminology that usually He sets our entrepreneur dreaming of seamless integration of the entire ecosystem or streamlining all the manufacturing process into a nice flow of things. Now it’s possible, but with technology, with this new era, there’s definitely things that can be happening. How do we get there? That’s the topic today. Usually starts by going paperless. So getting rid of paper is usually one of the first steps. We want to ensure that information stays within one system that we can view the information, make collecting the information way easier, gathering information, so that we can take advice and active decision live in the process. In this webinar, yes, we will be talking about that paperless shop floor and integration or tool. That’s an all-in-one tool that will connect your shop floors as if it would to be part of your office activities and everything else connected into the ERP.
How am I going to go through our webinar today? This is our little agenda. We’ll start by giving you a bit of a profile on who we are here at to repeat. Then we’ll walk very quickly, it should take about three or four minutes, to some of the 4. 0 concept like we just did, but just a bit more detail. Then we’re going through what I call this growth of manufacturers. But what I What I’m doing by that is I’ll put you in a few situations where we start with a smaller company to a bigger enterprise or how it grew through one to the other and how they have similar but a bit different challenges. And then for sure, how we will get to We’re going to get a little bit of a background in a little bit of a background where we solve these with the Genius shop floor. So a little history on Genius first. So what is Genius or who is Genius? I would say it starts with the team. So we have passionate people on our more than 100 people actually on our team, and we’re all aligned to serve our customers that aren’t manufacturers solely.
So really, our target is to get people on board with our system and get them striving and growing to where they envision their company. Where did we come from? Company history here. We were founded in ’89. It was a group of industrial engineers that were giving out services, actually, from the start. So we are really at the core of an engineering firm. And Then in ’95, it took four more into some release of manufacturing ERP portions of the system. Then in 2006, it really became a full solution with accounting and everything that took place. And then today, we have hundreds of company that trust into Genius and are striving with our business using our software. You can see on the left side, our footprint in North America. And as I said, 30 years in business, 100 plus employees for more than two, three, is it three years already? I think it is. Thousands of users throughout the North America. And I guess one of my preferred one is 96 % retention. On that one, really pretty proud of that one. If you look at the industry of ERP, there’s not so high numbers, usually. So we’re pretty proud of that.
That means people are coming to us and they’re staying with us. And I’m proud to say that a few weeks I saw this year’s number and we are still hitting that 96. What makes us unique at Genius? We’re built for custom manufacturers. So if you are a make to order, engineering to order, design to order in this type of business, it’s definitely you’re at the right stop for your ERP. We do have complete quote to cash. A little uniqueness here with our CAB to BOM, our integration with Solvents and to enter. We also have smart scheduling that’s pretty leading edge, and also a lot of KPIs and business intelligence to help you drive this decision making. Here’s a little picture of all of our feature in the system. I say all of them, but they’re not all in here. Basically, we go from quote all the way to work in process, shipping, APAR. We do have full accounting in there also. We We’re based on an SQL platform. I think the point here to say is we’re a one-stop shop. Everything is staying into one database. You can actually data mine and have information flowing, the point today where we say that we centralize information.
Yes, delivery mode. If you want to join in with Genius or get Genius, how can you install it or deploy it? You can actually install it, buy it, install it on your server or maybe on one of the hosting that you have, hosted servers. You can also rent it the same way. Or if you want, Genius offers a full SaaS solution where we can host it for you. All right. Not bad on timing. As I said already, there was a slide here where we were unique, how we differentiate. So might it be CAD2BOM, smart scheduling. We do have a lot of things on project management, live transaction tracking, a lot of visibility out of the system. You will find a lot of that information into our previous webinars. If you go on Genius ERP. Com on the resource section webinars, you will find a lot of these topics already recorded. We’ve made due diligence of doing webinars regularly in the past two years, three years now, almost one per month. So thank you for joining today also. All right, let’s get into the core of the heart of the topic today. What is 4. 0 so we can get to why is it so important to connect your shop floor with your ERP?
All right. Now, some of you might have joined us in October where I’ve used some similar slides. So bear with me for a moment. Since 4. 0 is really so much on topic today, I have reused some of the material that we did on our webinar about 4. 0 back in October. Not the same presentation, though, not the same topic. So I’ll reuse some of this slide, but I’ll summarize most of the information if you were there in October. It should go pretty fast. My objective today in the presentation is I’m going to go quick into some of the slides, and then we’ll have three story lines where I am going to show you example of different challenges in the industry and how, flipping over to a devil in the shop floor, we can solve these issues. All right, let’s jump into things. Summary of what is 4. 0. What are the concepts? Well, we’ll be talking about interconnection, first of all, meaning that machines, sensors, device, people, the ERP itself, everything now could be connected because of technology, because of this era in industrialization. Second of all, we’ll talk about information transparency. Since everything is connected, that means we can have operators, we can have machine feeding information, and have access to that information.
That means data transparency. That means also, I’ll stretch it to technical assistance. That means that if something needs to happen quickly, we could almost, with a certain set of parameters, have machines or people decide very quickly upon a set predefined of parameters. We’ll have decentralized decision. I think this is key to my topic today. I’ve put the shop floor actually right there on the top right where we say decentralized decision, because now, if we’re not talking static paper anymore, where probably today we’re giving out a stack, a packet of paper to our employees to work, but then three minutes later, it’s outdated. Well, with 4. 0, what we’re talking about is having an interactive screen in front of you where all the information is up to date, reviewed or changed in real-time, allowing people to take decision on the fly, people disconnected or usually disconnected, having all the information in front of us, enabling us to take key decisions. All right. What is 4. 0? It is the fourth era of industrial revolution. I’m going to go through it very quickly here. We rehashed this in October. You can go see it if you want more details.
What I want to focus on here is the paperless portion of things, because when it started on the first revolution, we’re back in the 1700. There’s no computers, so we’re doing a lot of mechanical stuff, and we have probably a whole lot of paper and files and everything to keep track of all. Then we get into the more the mass production of things, probably still a lot of paper. Maybe some of the punch cards Some of the stuff are starting to appear, but probably still a lot of people. Paper, sorry. Then comes the third evolution. Now we’re hitting the 1900 here. We’re starting to see more mechanical stuff, more automation come up, robots even. Then at some point, what is it, 1970s or ’80s, we’re starting to see computer. If you see at the bottom, I’m bringing it to a place where we start seeing travelers with barcode scanners, meaning that now it’s not just feeding information to your team, but it’s also capturing information back to a data system. Oh, so we can take more active decision then maybe three months later within a year, going through all of my papers I’m trying to figure out a trend.
Okay. And the last, not least, the fourth era where we talk about paperless connectivity, even machine learning, artificial intelligence and all this, that is basically 4. 0 manufacturing. What I’m showing here at the bottom is the paperless interface, interactive interface that we bring in with shop floor. Now, two, three slides just to show a profile So it’s a smaller company growing to be bigger and talking about the different issues or challenges that each size of company may have. As I don’t know the size of your company, I went through a few steps, a three-step thing where you can see it evolved. So it probably started out maybe in a garage, you started building a first product, a prototype or something. Then you start having a lot of quotes because it’s working. So, so many quotes, beginning to be too much for us. You know what? With the two last year, maybe buying our precut parts is not going to do it anymore. We probably want to cut our own pieces. So why not grow and buy a CNC, hire a third person? Why not? But with growth come challenges. We now have somebody that’s asking us all the time, what should I be doing next?
I don’t know your process. And then we figure out that, hey, she didn’t cut the proper pieces. We need to put that product aside, have whip that’s outstanding and start another project where we know we have the parts. And then we are managing these back and forth. But also back in the office, you’re starting to work on these quote and you’re figuring out, probably growing, that you don’t know where you’re making profit because you don’t know your exact cost, because you’re not tracking maybe labor hours and all that. So you are working a bit at a loss or at very general numbers. All right. At some point we grow or we’re looking at a different size company here, victim of our own success, and we We get to a point where we have multiple departments working together and all sorts of questions emerge. Let’s make the wheel go around first one time here. We have, for example, here in customer service, somebody calls in and ask for status of their order, or maybe somebody on the shop floor is wondering, What should I be doing next? What’s my next priority? Do I have everything I need to start working this job?
You know what? I can’t find the proper drawing. We’re probably talking about a packet of paper that was misplaced or that famous binder that I hear often about when we have a standard maybe sub-assembly or something like that we’re making often. I see this where, A, there’s a binder, it’s usually here, but it’s not today. So again, access to paper, we’re going to get back to that. We probably get to a point where we get pickers or people moving inventory around, and then they can’t find what they’re looking for. Qc guy or that gate management at the end of the flow where we check off on things. And there’s usually tons of paper. So even with the packet coming in, these guys probably have a form, a QC checklist, and all this. And the worst is that probably flows back to someone that needs to check things out, adjust things in the system, or enter stuff probably 24 hours later. So a bit too late to act on it. Again, you see where I’m going talking about connectivity of things. Oh, yes. And And there’s this guy in the middle that’s just wondering, I’m in the middle of task, but I can’t find where our whip things are located right now.
It’s not standard inventory, it’s just thing that’s in process. Where can I find it? And if you’re like a lot of our customers, and sometime or all the time, you have a bigger project that goes on for a month, tracking evolution of a project becomes critical, tracking your budget. So project management, project accounting and all that. Again, I’m all part of Genius, but this is also challenges that will be touched a bit today with our stories. And this is where I go. I hope I’m not too late. About 20 minutes in, that’s not too bad. And then we’re going to go into my three stories. How connecting Shopfloor with Genes here is going to help you. Real-life stories. I call it real-life, but these are all questions or things that I’ve heard working with different of our customers. Let’s go through it. Story number one, It’s the same thing we were seeing on the screen. Janet is calling, Hi, Frank. We expected to receive our order last week. Can you help me? I can’t find it. In my storyline here, my little robot, let’s say it’s me, Frank. I got I call from Janet and I’m wondering, who?
I need to get her status, sorry, her hoarder status. I’ll probably walk the shop and look at what I can find. Were the piece cut it yet or maybe See, go to the end of production, find out if it’s already cleared off, can’t find it, then I’m going to see if the parts were picked, and I’m going to go through some of these steps. I don’t want to bore you to this with a little robot going around. At the end, I get to shipping and I find out, Hey, they were But actually they were shipped yesterday and I sent you the paperwork over Frank. Oh, that’s true. I go back to my office and find out that the third paper in row in my pile is actually the order for Janet that just shipped out yesterday. I just didn’t get to enter it yet. So that’s probably close to some of the challenges that you guys are going through if you don’t have any RP or if you’re not that connected with your shop floor. So after going around like this, after eight different steps in the shop, probably an hour later, I actually had the paper on the corner of my desk, and I’m able to call back Janet.
But with all this, guys were talking to me about, Hey, I can’t find my drawing. There’s so much paperwork involved into all this. You just noticed it, Frank. You couldn’t even find the paper You have to walk around instead of just seeing it into your pile. Let’s talk about that. This is going right into the 4. 0 concept, connectivity, data, transparency, and it’s going even a bit more paperless and go real-time information gathering. How do we do that? Let’s actually finally go into Shopfloor from Genius ERP. Here is the Shopfloor interface. First of all, what jumps to the It is a web-based tool. That means I can use it on a lot of devices. Okay, it’s web-based. You could say mobile. I’m going to be careful here. You’re going to see what the size or the shape of it. I would probably suggest tablet for the size of the screen, not too much on a mobile. It will probably be too small, but that also means that you can use it mobile with a tablet or on a computer. It’s pretty flexible. Now, on top of that, we can We could have one station with a lot of people clocking in on the same station, or we could have each of your employees going around with their tablet and always connected real-time to the information.
Really, that’s up to you how you want to use it. Let’s go into some of our challenges. We have this person here that was wondering, I can find a drawing. What am I going to do? With Shopfloor, if we log on, I’m going to start with a very simple log on. What do I mean by that? This person has access to click, scan a task. We’re probably still talking of paper traveler or perhaps just a small sticker with a task on it or with a work order on it, scan it. As you see here, the task shows up already clocked in so we can start working. I said simplified login. You’re going to see there’s way less option than other people can have on my second or third I don’t remember. I’m going to show you the other login that’s more complete. So very simplified. I see my task. I can actually open and get information. Again, sharing information to allow decentralized decision to your team. So we have descriptions, quantity completed plan, maybe hours plan, hours remaining. So if you’re not the first shift to clock on this, how many hours do we have left to work to finish this off?
So so we know if we respect our budget or plan hours. But also to that question, I can’t find a drawing. Through here, I’ll have access to attachments. I can get into different sections of the software and actually click to see documentation. It could be a drawing, an assembly drawing, it could be work instructions, it could even be checklist, whatever we wish to share with our crew. Then by clicking Add, I can actually, if I’m on a tablet going around, I could take a picture, upload it, So again, link documents going both way from the office to the shop floor or people on the shop floor wanting to share information back to the office, either a key proof of deviations or whatever is happening on the shop floor. Now, I’m going to jump to the topic because I just said deviation. So it’s cool to have a picture of a deviation, but Genius allows you to track deviation with nonconformity report. So I could click here and actually log a nonconformity against this specific task or item. It comes up and already preselected on the task and item, and I can just specify which type of incidents it is, and then we can track what dispositions this position will do with this NCR.
All right. But on top of that, remember my QC manager or QC person was saying there’s so much paperwork. What am I going to do? So if we want to go paperless, I to feed that person with all the details that they need to do their work. It could be attachment like we saw earlier, but in this case, I also have access to reports. So it could be nonconformance reports. It could be nonconformance reports, it could be maybe a work order that I want to see the detail from, you can decide what forms or information you want to share with your shop floor crew and give them access to these reports through here so they can drill to a lot more information than what we have on screen here. All right. If we go QC, there is also a place where if they click here and there’s another webinar on this, we can get to a QC checklist where you can enter measurements that are required or maybe just go through gage or inspection points basically, and fill out these forms for each of your tasks. All right, are we done? Oh, there’s a key.
First question, Janet’s asking for status on her order. I was going to forget about that. Two things. As soon as I scan on my task, people are able to know right away in InGenius, because I’m selected on a task, that now, as you can see, I’m logged in as run, that run is currently working on this task right now. If I need to tell Janet where it is, if this person is working on its assembly here, so I can tell Janet, Yeah, it’s almost done. It’s at its assembly stage. It was 20 hours. We’re already two hours in, maybe two, three days. So again, you have the information for quick and exposed decision or answer to any customer, internal, external. The next thing I can do is report back so I can enter time. So this will tell me how much time I’ve been working so far. I can report on quantity, again, reject, and I could just complete everything and confirm, and that would close the task. In this case, I’m going to leave it open. I think I got another example with this one. I’ll just report time, we’ll leave it open. I’m going to confirm.
That means I’m I’ve not done, but I’ve entered time. I would scan back and forth again. It would have more hours on it, but still work to be done. Reporting time, people will see it in the ERP. We’ll see the progress bar, we’ll see, most important, we’re hitting work in process, cost in real-time also. Now I have labor entry against my cost. All right, let’s log out of this one. In my next example, we’ll go to another employee. Again, if you have questions as I move along, you can write them into the Q&A so we make sure to tackle them when we get to the questions at the end. All right, story number 2. Hi, Frank. It’s Tom from Richard, Oh, you know what? Tom is a great customer of mine. I need a replacement part and quick. Could you rush this order by any chance? Maybe some equipment’s down. He seems to be in a rush. He doesn’t usually ask for rush orders. Let’s Let me see what we can do for Tom. So Richardson’s in the buying. Let’s see if my little robot can go around and find what we’re looking for. So again, we’re trying to find a replacement part that we usually manufacture, so we’re going to be looking around.
Maybe we have some in stock. No, we don’t. Maybe there’s already some pilot for another order of shipping. Again, I’m going to just do this quickly. And probably your last step here is to wonder with executive team or maybe project managers, can we insert an order for Richardson with without putting in jeopardy another important order? So there’s sometimes politics involved or other forms of discussion that needs to take place that are not always just, let’s look at what we have and say, go, no, go. So after we finally come back, and for sure, we did all we needed to get a yes from everybody, we tell Richardson, Hey, Tom, I’ll get you your order. But going around like this, you’re probably disrupting a whole lot of the activities in your shop. Now, every people you spoke to are expecting that rush order to come in, but they don’t know when they will get the paperwork, if you’re still paperwork-driven. If they have a file where they have everything in order, they’ll always be on the look out. Then it came in. Where is it? Is it at the end or is it at the beginning?
So there’s uncertainty in the air, I guess. So that first person is wondering, What am I doing next? Am I starting on that rush order? And the same thing here. Frank told me about Tom’s rush order, but is Bob done cutting before me so I can actually start? Should I start on something else or wait? See, I’ve seen these type of disturbing questions from your team after somebody just walked around because we’re all expecting to do good things for our customers. There’s good values in the company, but now, how can we do this? Well, before I even go to the shop floor, there is a core solution right into Genius for a few of these questions. First of all, Genius has MRP, can tell you right away when you enter the order that material is available. Great. So I have all my material available. What’s the next step? He wants a rush order. That means I can’t just put it in row in the line of everybody else. I’ll need to test the waters. With Genius, I can do what if scenarios with my scheduling. I could crank this order up to maybe first place, second place next, and then visualize what’s the impact on the other jobs.
So then when or if I go to executive creative team, I can say, look at scenario number two. I think that’s best. Let’s insert it third place, and we should not put the other orders too much at risk. We had a bit of freedom in our schedule, whatever the case may be. What I’m trying to say is is already a portion of your solution. If you’re looking for smart scheduling, MRP, again, I would refer you to one of our past webinar on our website to know more. Now that this happened, we know we have stock. We’ve prioritized the order for Richardson as one of our priority. What’s going to happen on the shop floor? Let’s go back to our tool. Let’s say I’m Bob at cutting. I’m going to go P06. Here we go. I’m Roberto or Bob at cutting. Let’s say this was cutting. What’s the difference here? Right away, you see this person, instead of scanning, it’s already showing what station he’s usually working on. You You can see a list of tasks that is already in priority of your schedule. Right away, you can see I had some of these job numbers that were growing, growing, and one of these latest numbers on top, it’s for Richard because I’ve inserted that order as a rush above everybody else.
Now, I didn’t have to go on the shop floor and talk to Bob and tell him, Give me that paper, take this one instead, or put that in front. His screen is already up to date. As soon as we expected the simulation or the what-if scenario, the order bumped in front of everybody else on his screen. So live priority sorting of task. All right, but I guess there’s another question that’s for Bob. There was another guy on the shop floor wondering, Can I start on my next order? Is Bob done cutting yet? So if we’re the second guy in row here working on his list of tasks at the station, will he see the order that he’s expecting to see? We have a nice filter here that says, only show me task where the preceding tasks are done. If I untick this, I’ll see way more task So these are probably sitting at cutting or any previous step that there was before me, before my station. And when I hit this filter, I’m sure I’m not pulling on everybody. They said they are done. And as soon as they clock their time with that complete, it It shows up on my list.
All right. So that answers also the question of the other guys, Can I start working on this? He might see the next task show up a second, third, whichever, but as soon as Bob has done, it will show up on his list in the proper order. Another tweak In case you’re wondering, you might have a lot of things happening on the same day or on the same week. Short task. There’s also a way where your supervisor or team lead can come in and override the sequence for some of these tasks so he can sort out the order. Perhaps your scheduling is a bit rough and you’d want a team lead to override that sequence, very easy to do so on screen. Okay. Can we start? Do we have everything? All right. I think I’ve covered everything I needed for this example. We’ll keep that open and I’ll come back to it with my next story. Oh, Joe. Joe is one of our executive team member. Do we have everything ready to start phase 2 of our big project, and are we still on track with budget? That could be very complicated to some of our customers.
I remember talking to a few of our customers before they joined Genius, and there’s quite a bit It’s a challenge, usually, with these questions. I understand that from what Joe is saying, it’s a bigger project than usual, and now we need to check. We actually did it in phase. What do I usually do? Well, I’ll go see where they’re at, trying to gather information, We’ll look at stage. Again, I’ll make it quick with the little robot thing. What I think is probably most important in this question is, how are we faring with budget? Because without any RP, without any way of managing project budgets, evolution tracking, or without gathering information from the shop floor, you’re probably doing this by compiling paper, compiling entries, and it’s probably days later. I’ve You’ve even seen some company that they basically do it out of some a GL summary and some very rough numbers. So again, by having everything connected, you’ll bring the information and you’ll be able to have live budget tracking, live cost tracking. So coming back to the office with my probably pile of paper again and wondering what’s going to be happening next. The first portion of the solution, again, here is, yes, we do have MRP in the system.
So when I get to phase 2, I’ll see if I have everything available. Also, as I said, we’re tracking budget, we’re tracking everything going through, and that’s what we’re going to see again with the shop floor tracking connectivity, how we can get everything happening in the system live. What question do we see appearing often in this situation? Do I have everything needed to start phase two? It’s great that the guy in the office, Frank, looking at the project, I can see it, but there’s a guy on the shop floor about to do his ask, is he aware that he has everything he needs? On the other side, there’s probably also somebody picking that’s wondering, where did they put this? I mean, you grew. You’re at a point where somebody’s receiving, somebody else is taking, putting back. So we probably want to know what location it’s in right now. And again, that person that’s always the second run in row, he’s now looking for the part. Great, that Bob has done, but where did he put it? Where can I find the pieces? They’re not stock items that I’m managing in an inventory. It’s just ongoing whip.
So how can I locate that? All right. And the last question being the one I already voiced about budget hours. So let’s go back in shop The first thing I’m wondering about is that person sitting at the CNC machine wondering, do I have everything I need to start working? So that’s actually my next filter. See here on hand, If I remove it, I do have an availability context with everything on hand. But here I have a task where if I try to start, I’m short, I’m missing components. If I hit that filter, that is usually the standard way we would have you set up for using Jean-Claure, everything is on hand and it is up to my turn to work. So this is all the things that I can start set up, I can turn around, I have the goods, I can start working. I’m ready to work, ready to build. All right, so I can usually go I’m going to go ahead and start working. Oh, and let’s send that guy the press, and I’m looking for the parts that Bob has cut before. See here, I have a location. I’m able to locate my whip.
As I am working, let’s say, I can check out different jobs, I can actually click Well location and actually come in here, change the location of where I am putting the with or the ongoing work and process goods. I’m enabling my members to find it quickly when they are looking for it. The next thing is, remember that guy on top that was looking for bearings? Now we need to pick what we need to… The components as I am selected on a task, I can hit batch consumption. That screen that opens up is actually my full pick list already ordered or sorted by location. It’s already optimized to for me as a pick route. Let’s talk about row number one. Let’s pick whatever I need in row number one, and let’s hit bin be something or row number two afterwards, and I can flow down and pick everything I need. Now, all these buttons are green because remember, I had that filter with everything on the hand, so now everything’s green here. You could have a situation where maybe some of the parts are missing if you’re going to pick early, and you would see the other colors coming also.
When I hit this button, it picks inventory, so it depletes inventory in real time and puts the cost and whip in working process. So I’m seeing progress on my budget, I’m seeing progress on costing. And live, I know that inventory went down a bit, so it could trigger purchasing, it could trigger replenishment and all that. All right. And it’s disappearing from my list, so I can make sure that I take care of that entire list before going up to work. Okay, what am I missing here? Yeah, tracking budget also means tracking manpower. I’ve done it before where you saw me go in and clock, enter time. Same thing here. I could click Enter time. I could be clicked on one or multiple tasks. This is actually why we see a grid here. Let me do the example. I could be selecting three different tasks. Let’s say you have a lot of small tasks. You don’t want to be going back and forth to your tablet or station. You could say I’m working on all of these three. Got up to work, come back after lunch or before leaving and say Enter time. Then we have rules of how we can parse time across your different the task, either evenly or maybe a pro rate of planned time or otherwise.
I can complete everything and say, great, I’m done, and it will complete the task, get them off my list, but also it signals everybody in the office that this is done. Perhaps you’re early, or perhaps you’ve used more time than planned, but you’re telling everybody that, Hey, I have plan hours. They went down. My actual were actually better than my plan hours, but we’ll see all the comparison, and we’ll see the stress of all that happening live. All right. I think that goes really around my example. Sorry. Oh, the last thing. If I want to report that everything is done, now, probably today, If you have this traveling sheet that goes back to the office, perhaps even with a QC sign off and everything, and then somebody close off everything in the system so it can go to stock or it can go to shipping or whatever next, you’re also able to close work order straight from that screen. I can actually select the work order and just say close it off, and it will close all the paperwork for production and actually generate inventory and all that, so it can be ready for shipping, invoicing, and all that.
All right. So again, if you ask me what is 4. 0, it’s peace of mind. It’s having everybody connected so they can do their work efficiently. So again, interconnectivity, paperless, data transparency, decentralized decision. The point here is make sure the information flows to a system so that we can get alerts, we can get people to re hack, we can have exposed decision on the actual status of everything and be equipped to take our company to the next level, basically. And yes, that can all happen in Genius. Again, you saw it with project management, with scheduling, with the shop floor tool that just show you now it’s not just It’s feeding the shop crew with information. It’s feeding the information back to the office also so everybody can work as one. All right. Oh, that’s a list of the features that are included in shop floor. Again, paperless, flexibility, quality control, capturing pictures and all that. So maybe you want to look at this page on pause after reviewing our webinar next time. So really, at the end, what we’re meant to say here is if everything is streamlined as much as possible with everybody connected, now you can put your energy at the right place.
Maybe work on things that are more important than clerical or paper filing. You see where I’m going with this. Always makes me laugh. What’s coming up next with Genius? We do have, for those that are aware, a thought aware, sorry, we do have a platform where we have training videos and training sessions. So if you want to If you want to know more about the shop floor tool, the paperless shop floor tool, we do have a session coming up on June 7. It’s going to be two session of two hours, a live session with a presenter, with a teacher. Again, to get access to that, you have to be one of our Genius academy members. Now it’s time for question. I see we have one or two. Because it’s a web version, how does it work for licenses? Okay, so actually for licenses, it’s a package for a certain number of employees. We are really going by number of employees for the licenses. Let me read this correctly here. I think there’s more questions that I’m not seeing here. Give me just a moment to read it. If we close the job, can it still be modified by QC?
Yes, actually, yes. Maybe I can try this, but if I untick the uncompleted, you can see my tasks are reappearing. I can always go back, view documents that were attached, create NCRs against closed task, So yes, I can consult, complete a task or history information. There’s other function that I didn’t go to detail today. Actually, you make me think of a good thing, Lisa. There is another thing that we can do here, perhaps some of our future customers are wondering, maybe I don’t have routing today, maybe I don’t have the capacity or the bill materials or structure with task. Don’t worry, we can add a task just from a work order and you could define what type of work is being done on the fly. You do not have to have all these tasks predefined to be able to scan and report time or view information. If you just have a job number, a work order, documents attached to that, yes, you could scan it in, to create the task, and you would get access to attachment and creating CRs and all this and/or time as well. So yes, very early on without routing, you would be able to leverage this tool.
Any other questions? Please fire away. All right. Then if you need to reach us with other questions or follow-up, don’t hesitate. If you’re already in contact from somebody with Genius ERP. Please continue communication with this person. If not, I invite you to write directly to me or to say hello at Genius ERP, and we’ll direct your call or your inquiry to the person. You probably already know the access to our website. Since you’re at this webinar, you have to register to it. But also there are some great insights on Genius ERP Insight on YouTube. If you look for that wording here, Genius ERP Insights, you’ll find a few videos. I’ve just posted one recently, exactly on the topic from today. In a three or four minute session, we go through all the features from Shopfloor. Feel free to go take a look if you want. Thank you for joining, everybody. I wish you a great day.
Get your eBook Scared to implement a new ERP?
"*" indicates required fields